Wissenschaftler experimentieren bei 3000-facher Erdbeschleunigung

FAU und Schaeffler entwickeln neuartigen Hochleistungsprüfstand
3000-fache Erdbeschleunigung: Unter dieser extremen Bedingung und den daraus folgenden hohen Belastungen testen Wissenschaftler der FAU künftig Wälzlager. Hierfür hat der Lehrstuhl für Konstruktionstechnik der FAU in Zusammenarbeit mit Schaeffler einen bisher einzigartigen Wälzlagerschleuderprüfstand (WSP) entwickelt, um das Verhalten von Material und Konstruktion der Lager genauer zu untersuchen. Die Ergebnisse dieses Forschungsprojektes sollen die aktuelle Wälzlagertechnologie optimieren -mit dem Ziel, den Kraftstoff- und Energieverbrauch bei Fahrzeugen und Maschinen zu verringern.
Wälzlager: ein altbewährtes Prinzip made in Franken
Wälzlager sind allgegenwärtig in der Industrie, aber auch im Alltag. Denn kein Rad dreht sich ohne sie, kein Motor würde laufen, kein Getriebe funktionieren. Sie bestehen aus einem Außen- und einem Innenring, zwischen denen Wälzkörper angeordnet sind. So liegt die Achse eines Rades auf dem Innenring und übt dort die Belastung auf die Wälzkörper aus. Das Prinzip solcher Lager war vermutlich schon den Römern bekannt, wurde spätestens aber von Leonardo da Vinci im 15. Jh. vollständig entwickelt.
Das europäische Herz der Wälzlagerindustrie schlägt in Nordbayern
Mit der Erfindung der sogenannten Kugelmühle in Schweinfurt Ende des 19. Jahrhunderts konnten erstmals spezielle Kugellager in industriellem Maßstab gefertigt werden. Dies markiert den Beginn der Wälzlagerindustrie, deren europäisches Herz auch heute noch in Nordbayern schlägt. Bei den Lagern, die der Lehrstuhl für Konstruktionstechnik der FAU auf dem WSP untersucht, handelt es sich hauptsächlich um sogenannte Nadellager. Zwischen den Ringen laufen hier zylindrische Rollen, jedoch sind diese im Verhältnis zu ihrem Durchmesser sehr lang. Sie kommen zum Beispiel in Fahrzeuggetrieben zum Einsatz.
Ein tonnenschwerer Prüfstand
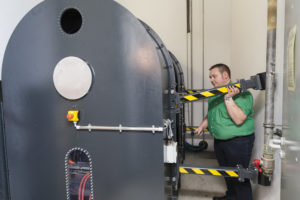
Insbesondere das Reibungsverhalten von Wälzlagern bei solch hohen Fliehkräften, wie sie auf dem WSP erreicht werden, ist bisher wenig erforscht. Um die extremen Belastungen, die auf das Material und die Konstruktion dabei wirken, zu untersuchen, hat der Lehrstuhl für Konstruktionstechnik der FAU zusammen mit Schaeffler nun ein neuartiges Testverfahren entwickelt. Die sich hieraus ergebenden Fragestellungen sollen damit sowohl experimentell als auch simulationsbasiert untersucht werden.
„Mit Hilfe dieses Prüfstands haben wir nun die Möglichkeit, die Phänomene an einem Wälzlager im Fliehkraftfeld besser zu verstehen. Ein wichtiger Aspekt für uns ist hierzu die weitere Verbesserung unserer Simulationswerkzeuge für Wälzlager auf Basis der Versuchsergebnisse. Hiermit können wir die gewonnenen Erkenntnisse auf anwendungsnahe Bedingungen übertragen und somit unsere Produktentwicklung weiter verbessern“, führt Oliver Graf-Goller, Projektleiter seitens Schaeffler, die Bedeutung des Prüfstands aus.
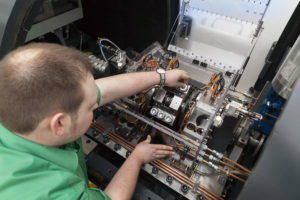
„Leichtbau und Energieeffizienz sind heutzutage zwei entscheidende Punkte bei der Entwicklung neuer Fahrzeugbauteile. Verbesserungen lassen sich im Nachhinein dann ganz konkret an einer Verringerung des Kraftstoffverbrauchs messen“, erklärt Dr. Stephan Tremmel vom Lehrstuhl für Konstruktionstechnik. „Vor allem die Frage, welche Faktoren die Lager unter Extrembelastung beeinflussen, können wir an unserem Prüfstand untersuchen. Solche Faktoren können beispielsweise Temperaturen, Beschichtungen oder geometrische Details sein.“
Etwa die 400-fachen Belastung eines Kampfjetpiloten
Für ihre Experimente haben die FAU-Forscher zusammen mit Schaeffler einen Prüfstand entwickelt, mit dem die Lager das 3000-fache der Erdbeschleunigung erfahren können. Das entspricht etwa der 400-fachen Belastung eines Kampfjetpiloten.
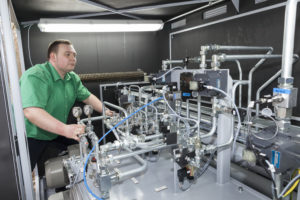
„Die Lager selber drehen sich hierbei gleich zweimal. Mittels eines sogenannten offenen Planetengetriebes rotieren die Prüflinge, gleich den Planeten unseres Sonnensystems, sowohl jeweils einzeln um ihre eigene Achse, als auch nochmals in ihrer Gesamtheit um eine Zentralachse“, erklärt Tremmels Kollege David Hochrein das dahinterliegende Prinzip.
Der FAU-Wissenschaftler hat den 16 Tonnen schweren Prüfstand, der in einem eigenen Prüfbunker auf 22 Quadratmetern untergebracht ist, bis auf die letzte Schraube entworfen und mit den Mitarbeitern der Zentralen Mechanik- und Elektronikwerkstatt der Technischen Fakultät der FAU in die Realität umgesetzt.
Prüfstand und Computersimulation
Doch mit dem rund 800.000 Euro teuren Projekt verfolgen die FAU-Wissenschaftler noch einen weiteren Zweck. Zusammen mit den Partnern von Schaeffler wurde eine für wichtige Simulationsverfahren nötige Software verbessert und weiterentwickelt, mit der schon vor dem Bau eines Prototyps das Verhalten der Wälzlager simuliert und somit schon am Computermodell optimiert werden kann. „Der WSP, der in der Fachwelt ein Novum darstellt, dient damit nicht zuletzt einer Überprüfung der Berechnungen und virtuellen Modelle. Wir erwarten letzten Endes aber durch den Prüfstand und die verbesserten Computermodelle einen erheblichen Erkenntniszuwachs bezüglich des Reibungsverhaltens von Wälzlagern unter Extrembedingungen“, führt der Lehrstuhlinhaber Prof. Dr. Sandro Wartzack das gemeinschaftliche Projekt näher aus.
Weitere Informationen:
Dr. Stephan Tremmel
Tel. 09131/85-23222
tremmel@mfk.fau.de